The German company has partnered with cleantech firms to build an ammonia cracker that could produce emissions-free hydrogen at industrial scale.
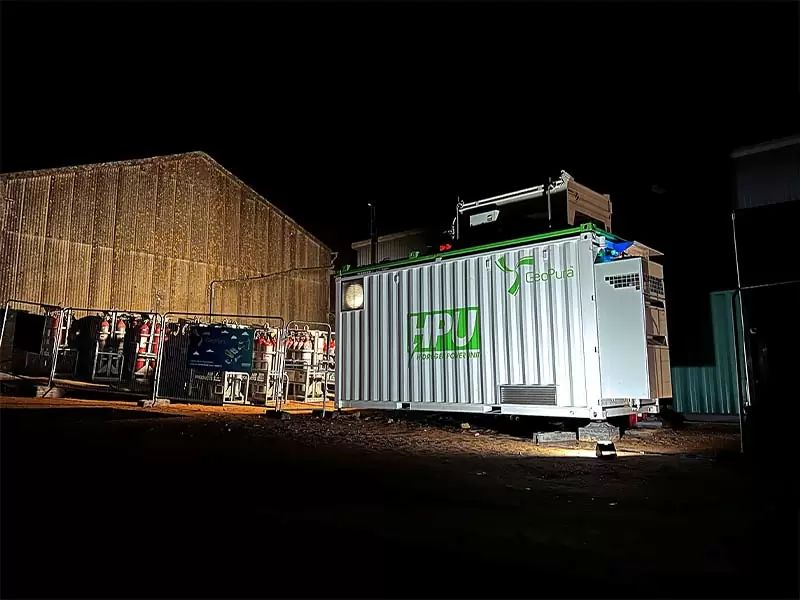
Once the factory in Newcastle in northeast England was where Siemens Energy built steam turbines for use in coal-fired power plants. Now it has become the location of an experimental facility to create green hydrogen through ammonia cracking — a process that could be the key to establishing a clean energy ecosystem for the renewable fuel.
Siemens Energy is building a prototype ammonia cracker that will produce 200kg of hydrogen a day to power buses and trucks. The clean fuel will also be used for off-grid electricity generation to replace diesel generators.
Producing green hydrogen at scale is a tough nut to crack because separating hydrogen from water through electrolysis requires a large amount of energy. Ammonia, on the other hand, has a high concentration of hydrogen, takes less energy to extract and is readily transportable in bulk. A number of companies are investigating setting up ammonia-cracking facilities, including a project announced this week by the Port of Rotterdam Authority in the Netherlands.
What is novel about Siemens Energy’s £3.5m project is its use of a metal membrane technology designed by Fortescue Future Industries, an Australian green energy technology developer, to produce high-purity hydrogen required for fuel cells.
The membrane technology, which acts like sieve through which only hydrogen can pass, is what gives Siemens Energy’s prototype an edge over other ammonia crackers, says Zac Cesaro, program manager of ammonia cracking and efuels at Siemens Energy. “We think this is the most competitive technology to use,” he says.
An internal venture
Although Siemens Energy has a corporate venture arm, the idea for the ammonia cracker emerged internally. It is partnering with both Fortescue Future Industries and GeoPura, a UK renewable off-grid energy generation manufacturer, which will both provide technology and customers for the renewable fuel.
Siemens had already worked with GeoPura on the development of a hydrogen fuel cell, making it a natural external partner in the venture, which it may spin out as a new business in the future. It also collaborated with its venturing unit and Innovate UK, a government agency.
“Venture building for us at the moment is all about collaboration and co-creation,” says Julia Reid, communications partner at Siemens Energy Ventures, the company’s CVC. “We always try to partner with others, partly because we know then that there is an interest, and it is safer bet. The pooling of resources means we can do this quicker and get these solutions to market more quickly.”
Challenge of making ammonia production greener
Siemens Energy will use power from the grid to heat the ammonia for the cracking process. It plans to buy renewable energy through power purchase agreements to make it fully green. In future it will use waste heat from the ammonia cracking in a self-contained system that will require little external power.
The hydrogen from this first prototype will be used by partner GeoPura to supply its hydrogen power units, which replace diesel generators as an off-grid zero emissions-power solution for industries including TV production, construction and outdoor events.
The system will also produce enough hydrogen a day to power between five and 10 hydrogen fuel-cell electric buses. In future this type of decentralised ammonia cracker could be installed at hydrogen refueling stations for buses and trucks, as well as at train depots that are being retrofitted to power hydrogen-powered trains.
Siemens Energy’s prototype is specifically designed for transport and off-grid uses, but larger centralised crackers are also being developed to bring hydrogen into pipelines for heating homes and for industrial use. Germany has announced plans to build green ammonia import terminals that will be an emissions-free alternative to imports of liquified natural gas.
A challenge of scaling the technology is the sourcing of green ammonia. Manufacturing ammonia is energy intensive and is made almost exclusively from fossil fuels.
This may soon change as several green ammonia projects are under construction in areas where renewable energy is plentiful such as Australia. One big cost saver is the fact that infrastructure for transporting and storing ammonia is already in place. “Because we have ships and import, export terminals around the world, we know how to handle ammonia industrially,” says Cesaro.