Heavy industry accounts for 22% of global greenhouse gas emissions but is notoriously difficult to decarbonise. These startups are developing solutions, from new thermal energy storage and fusion reactor design to emissions monitoring.
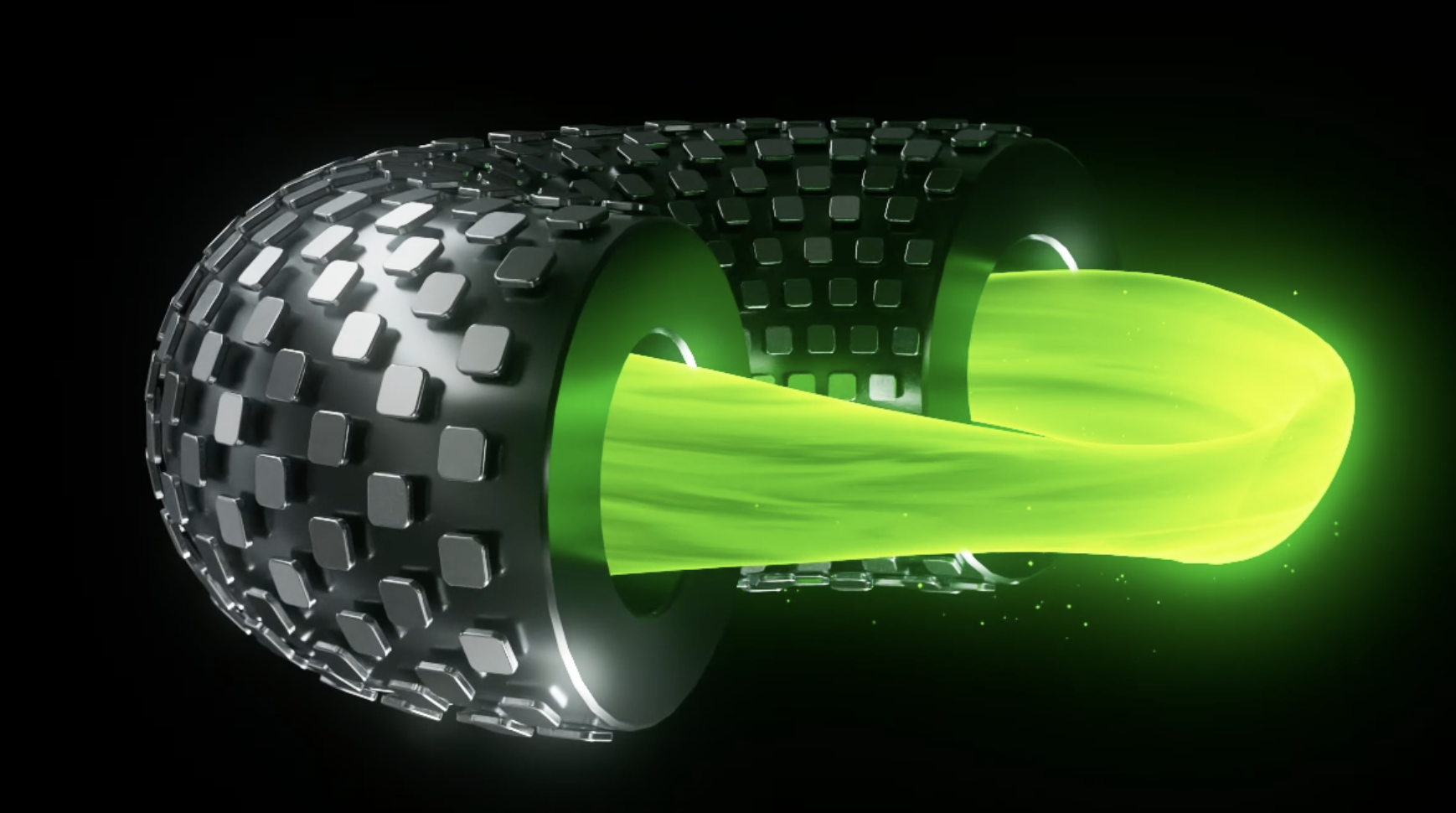
Heavy industry is responsible for 22% of the world’s greenhouse gas emissions and is considered one of the most challenging sectors to decarbonise. Clean energy solutions such as battery storage, renewable energy and hydrogen are often not viable or even available at the scale heavy industry operators need. Mitigation technologies such as carbon capture are still very expensive to run.
But a number of startups are working on technologies that may help. These companies are not often in the limelight — they tend to be the kind of B2B businesses that don’t feature often in the media. But many of them are already working with industry partners to test and validate their solutions. The Energy Council at Global Corporate Venturing presented a showcase of some of the startups that their members are working with.
Many of these young companies seek new partners to run pilot programmes with and they are raising funding rounds to scale up and commercialise their businesses.
Here are the startups to watch from that showcase:
AIS Field
This Turkish startup has developed a robotic system to carry out the dangerous work of inspecting oil storage tanks. Tanks often have to be drained for maintenance work, an exercise that can cost energy companies some $2.5m in downtime. The RUVI Oildiver robot, however, is designed to be submerged in oil and can carry out maintenance while the tank is full. With more than 100,000 storage tanks worldwide, the potential market for this is large.
AIS Field has been working with Tupras, the Turkish oil company, to test the patent-pending technology and is seeking other strategic partners and investors. The team would like to raise $1.5m to expand its commercial team and accelerate international expansion.
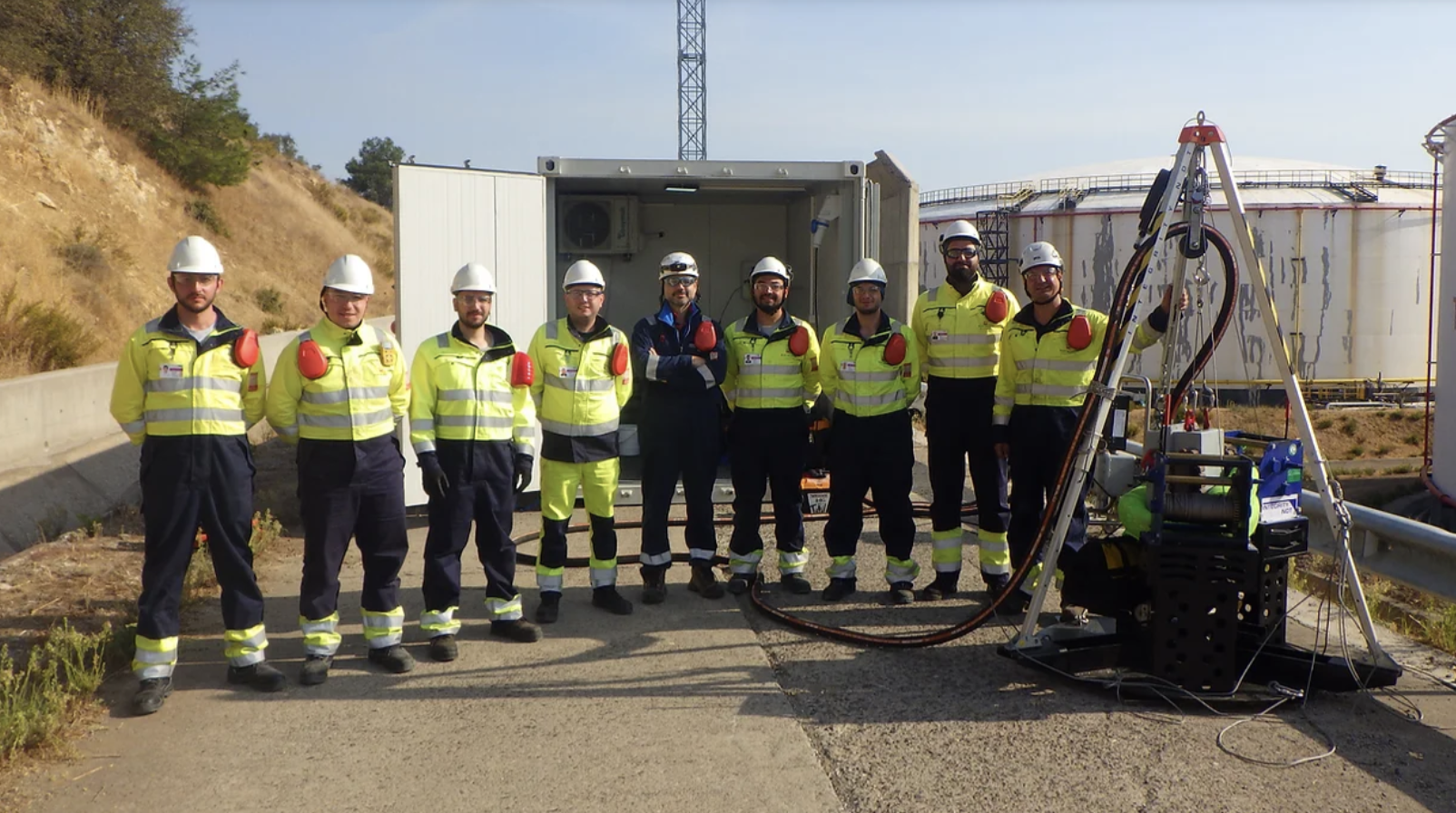
Ardent
Capturing carbon at industrial facilities is the most effective way to decarbonise heavy industry but doing this efficiently is still a challenge. US-based startup Ardent has developed a membrane technology that can separate pollutants from the air at lower concentrations and in hotter and wetter conditions than has been possible before. The company believes this can help bring down the cost of point-source carbon capture.
The team has pilot projects with companies in the steelmaking, kilning and petrochemical industries. It says it can bring out the product commercially by 2026. It is raising a series B funding round and wants to undertake more pilot projects with industry partners.
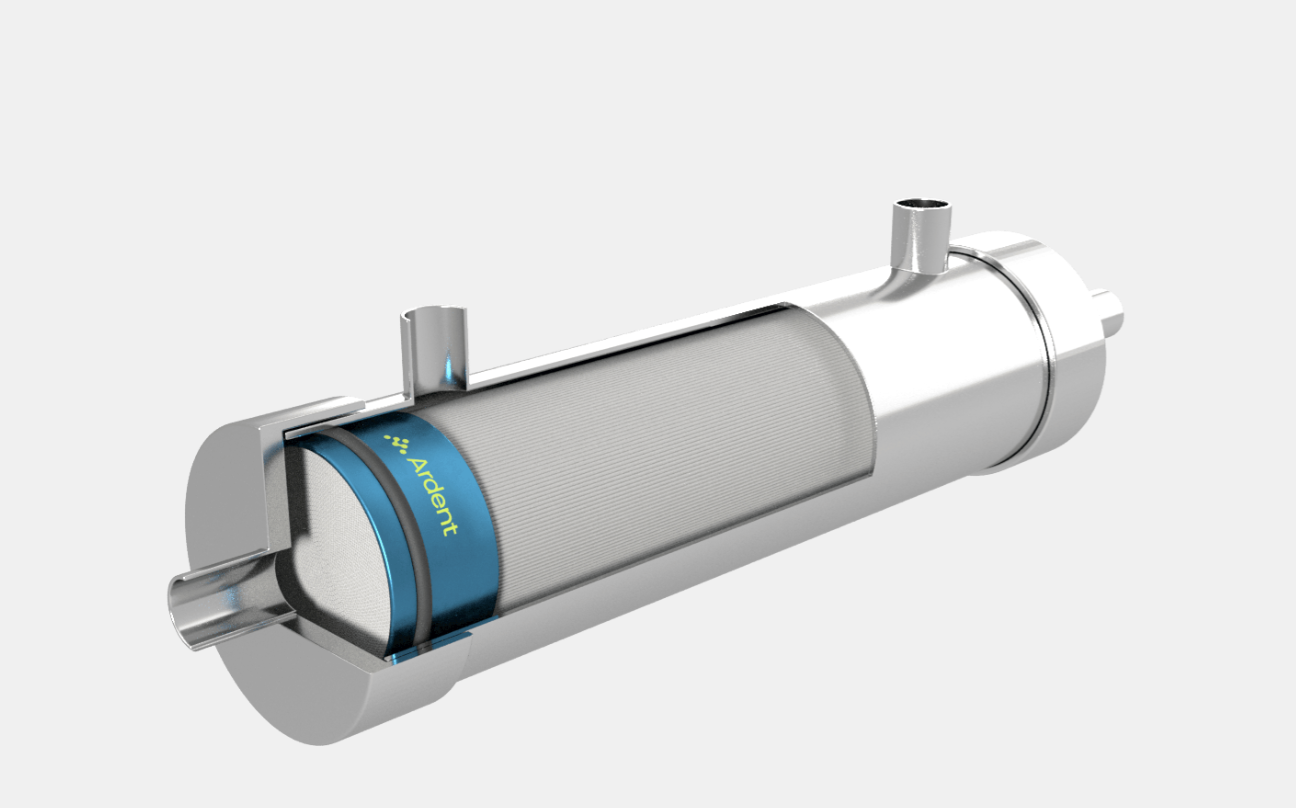
Einsted
Transitioning to using hydrogen as a fuel source is a key part of the decarbonisation agenda but producing hydrogen is still expensive. Argentina-based Einsted has developed a technique to convert methane into hydrogen and carbon nanotubes using ultra-fast plasma pulses. Einstein says that this method is between three and ten times faster than existing hydrogen electrolysers, and creates 30% more energy. Because it operates at room temperature, rather than requiring high heat, this makes it energy efficient.
The company, which has a team of 18 people, has a pilot with Vista, the Argentinian energy company, which is also an investor in the company. The team is seeking to raise a $1.2m funding round to take the technology forward.
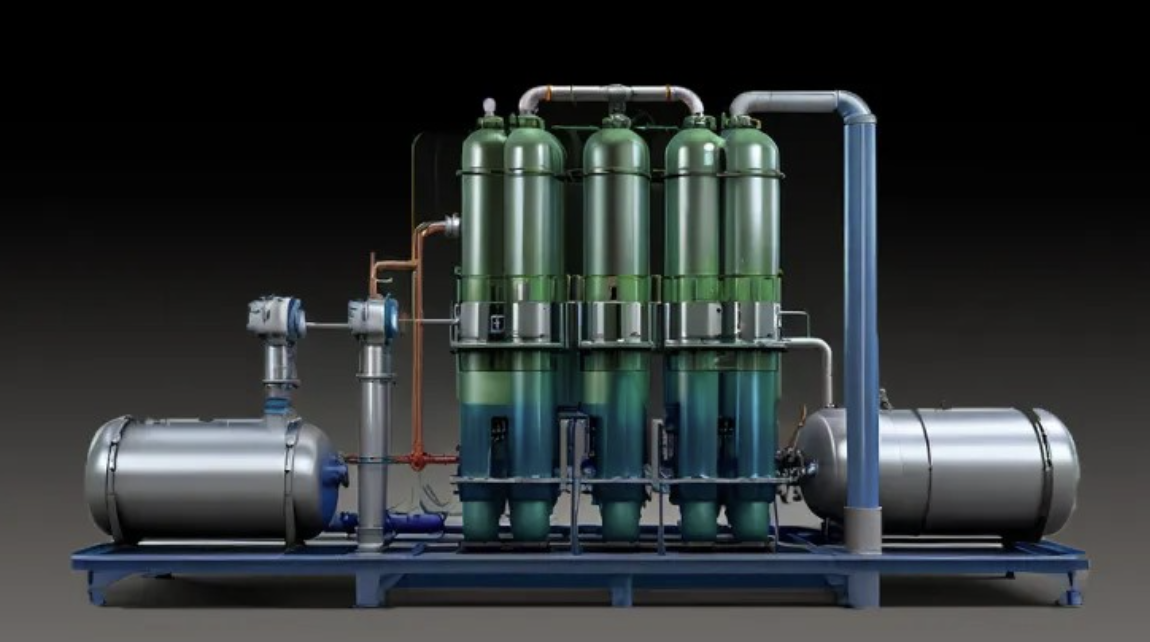
Electrified Thermal Solutions
One of the reasons that heavy industry struggles to switch to a zero carbon energy sources is because it needs very high temperature heat for its processes, which is difficult to produce with alternative energy. Electrified Thermal Solutions, an MIT spinout, has developed a system based on electrically conductive firebricks which can take renewable energy — from solar, wind or elsewhere — and deliver it to industrial users as a hot gas with a temperature of around 1,800 degrees celsius.
The company claims the system is three times cheaper than any green hydrogen approach. Electric Thermal is running an elevator-sized demonstration unit but is looking to raise money to scale up these units to be able to handle thousands of megawatts of energy. The team is about halfway to raising a $20m funding round for this scaling up project.
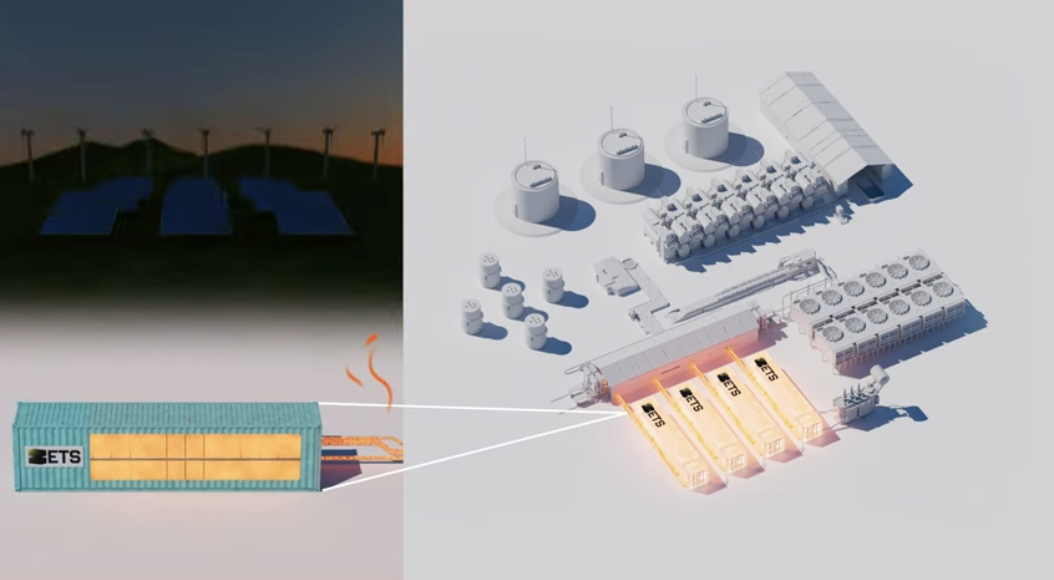
Mirico
Measuring emissions such as methane is another headache for heavy industry. It is hard to cut emissions if you can’t tell exactly where they are coming from and how much is escaping. Mirico, a UK startup, is hoping to address this problem with a laser spectroscopy system that can monitor an entire industrial site’s emissions with a high degree of precision, even in poor weather.
The company has validated its technology with Shell, the Anglo-Dutch energy company, and recently raised a $2m seed round. It is seeking to raise a $5m series A round to improve the products and increase customer uptake.
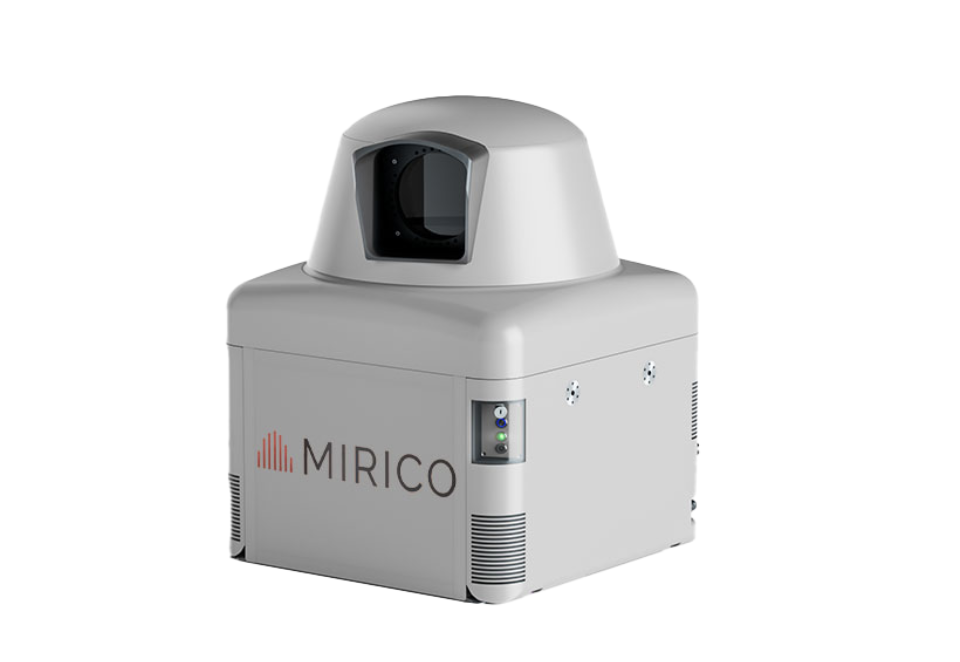
Thea Energy
Nuclear fusion is another of the great hopes for unlimited clean energy. Stellerators are seen as one of the leading ways to achieve these controlled reactions. But these complex rings of magnets are notoriously difficult to manufacture. Thea Energy has developed a new type of stellerator architecture, consisting of arrays of flat magnets that can be dynamically positioned to create exactly the shape needed. The team says this means it can advance more rapidly than other fusion companies and at lower cost.
The startup, which was spun out of Princeton University and Princeton Plasma Physics Lab, is seeking to raise a series B funding round to help it build an integrated stellerator system by the end of the decade.
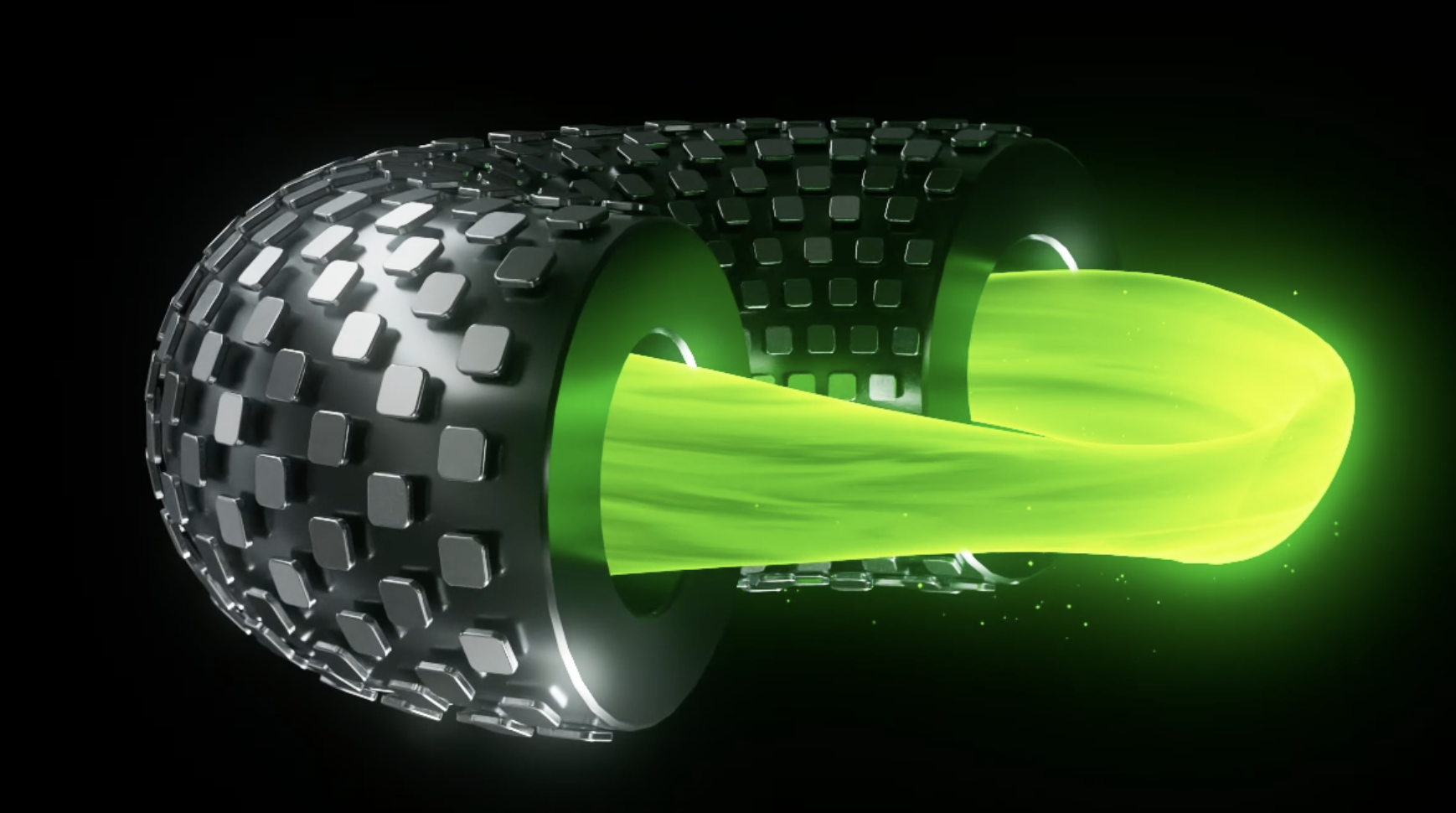
Wase
This UK startup has developed a way to speed up the process of turning food industry waste into biogas for energy. At the moment this is mainly done through anaerobic digestion, a process that is still relatively inefficient, time-consuming and requires bulky storage tanks.
Wase’s solution is an electro-methanogenic reactor in which electrodes containing membranes of electrically active bacteria create a reaction that breaks down the waste and releases electrons.
Wase says the system can achieve between 70% and 80% conversion of the waste to methane, compared with between 50% and 60% for a typical anaerobic reactor. It says it is between three and 10 times faster than current anaerobic digestion systems, creates 30% more energy and needs a 70% smaller footprint for the reactor.
The system is being tested by a number of dairy farms, breweries and distilleries, but Wase is seeking more industrial partners to work with.
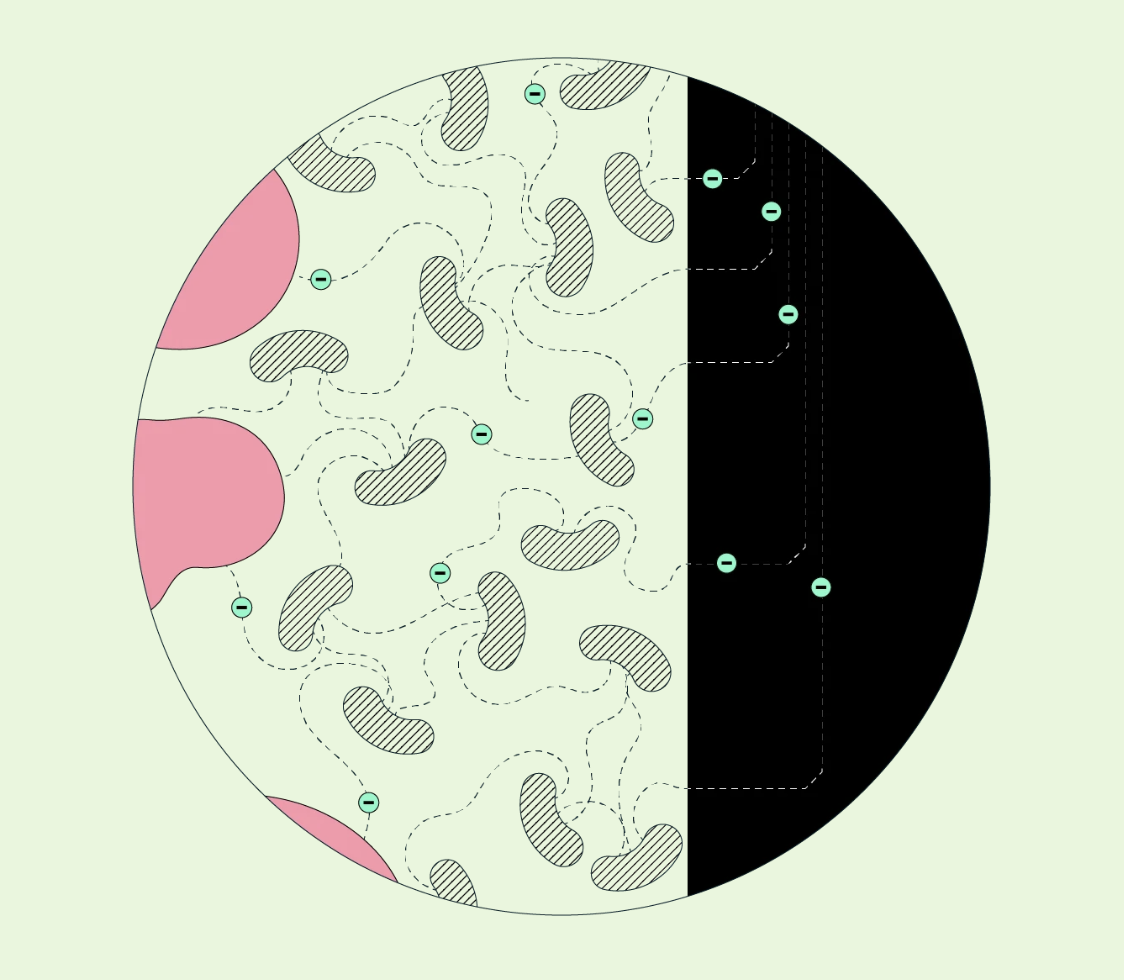
See the full pitches in the video below:
Find out more about the GCV Energy Council here.
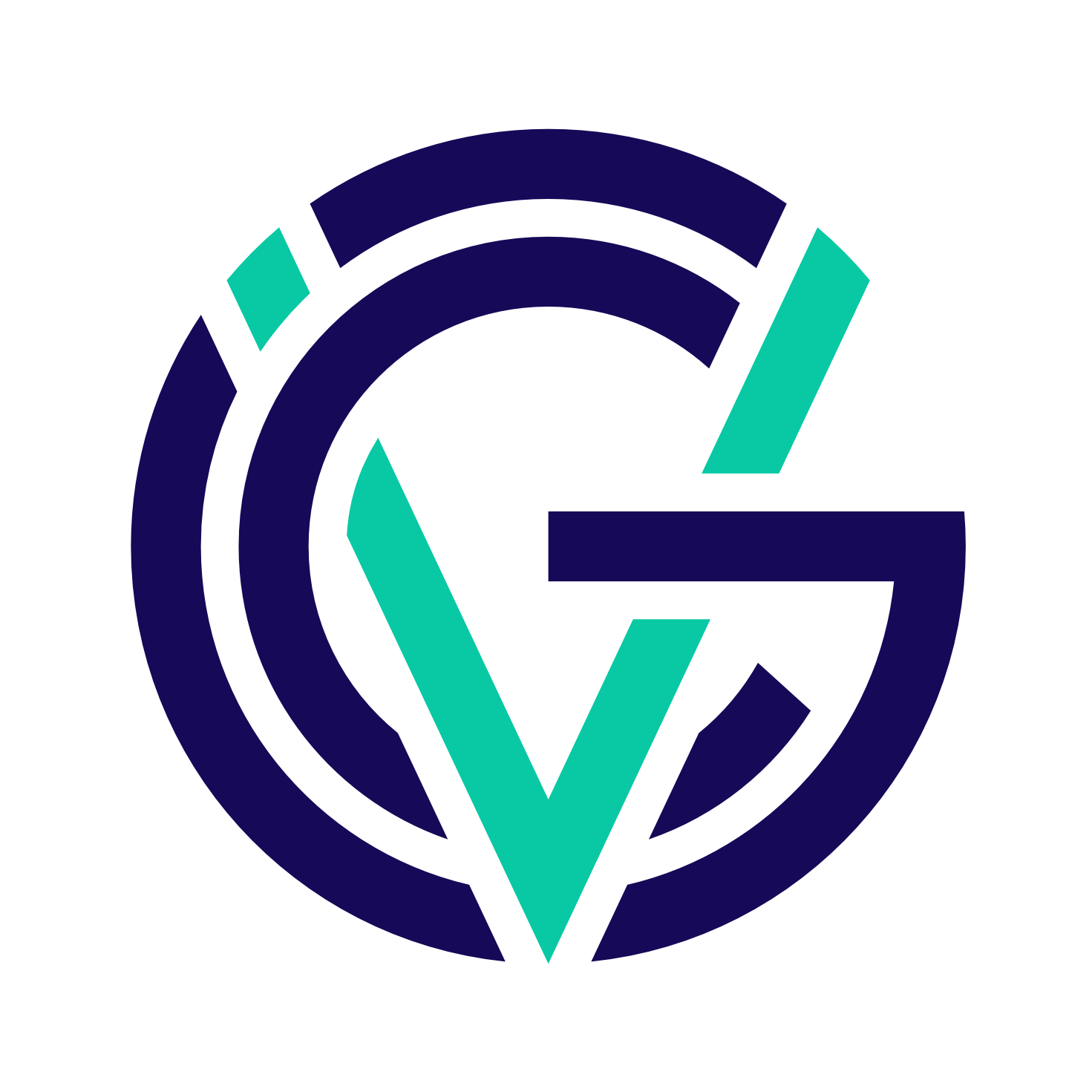
Maija Palmer
Maija Palmer is editor of Global Venturing and puts together the weekly email newsletter (sign up here for free).